Posts Tagged #behind the scenes @ the henry ford
Capturing a Moment: How We Created a Display for Henry Ford’s “Sweepstakes”
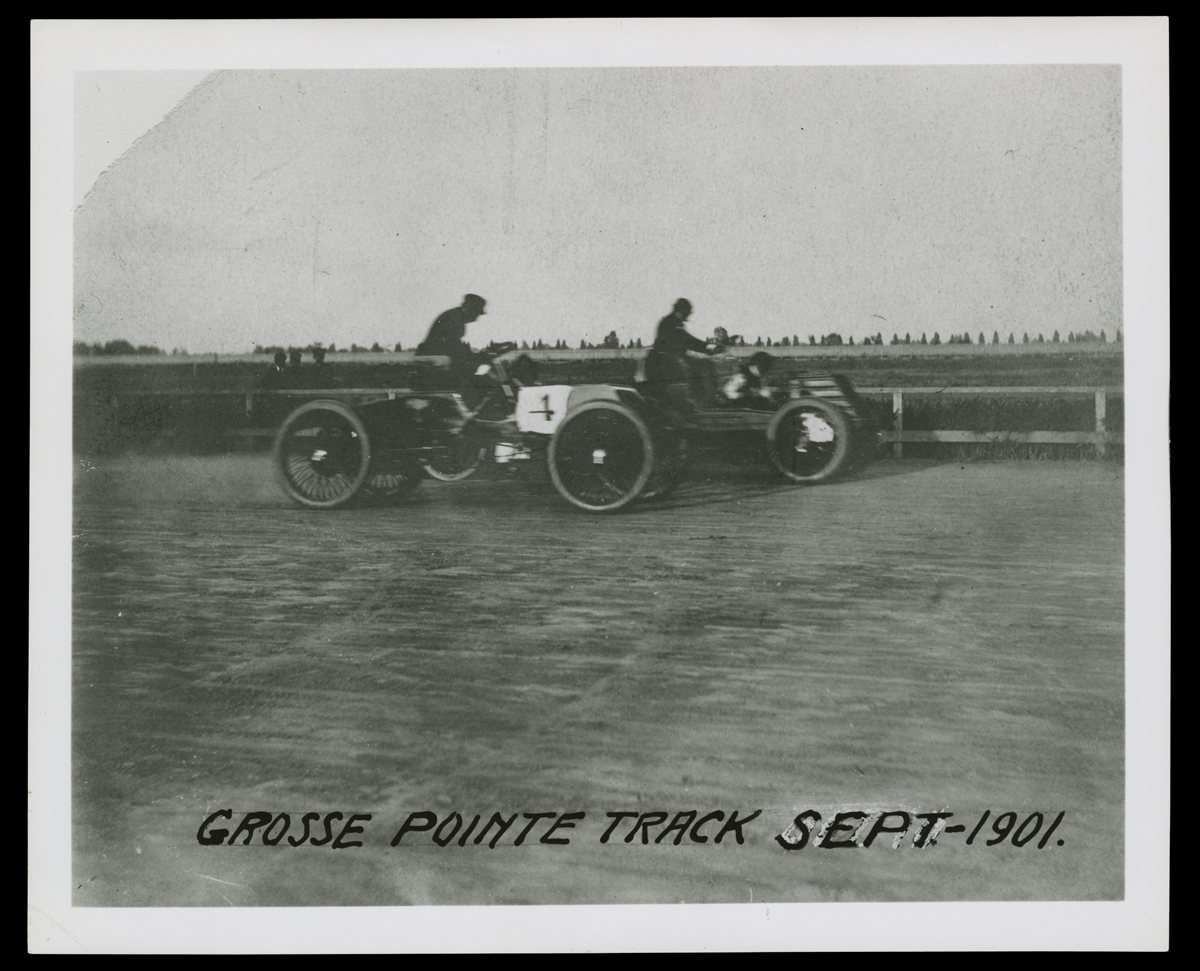
In his first race ever, Henry Ford beat Alexander Winton in the Sweepstakes Race. / THF94819
On October 10, 1901, Henry Ford made history by overcoming the favored Alexander Winton in his first-ever automobile race. Backed by a willingness to take risks and an innovative engine design, Henry earned the reputation and financial backing through this one event to start Henry Ford Company, his second car-making venture.
His success that day is a natural introduction display for our newest permanent exhibition, Driven to Win: Racing in America, presented by General Motors. Driven to Win celebrates over 100 years of automotive racing achievements and the people behind the passion for going fast.
Photos of the 1901 race provide a view of the environment that written accounts don’t. / THF123903
In creating an exhibition, we start with many experience goals. In this case, one exhibition goal is to take our guests behind-the-scenes and trackside. As you experience Driven to Win, you’ll find many of the vehicles displayed on scenic surfaces and in front of murals that represent the places the cars raced. Henry Ford’s Sweepstakes Race took place on a horse racing track in Grosse Pointe, Michigan. Through reference photos and discussions with our exhibit fabrication partner, kubik maltbie, artisans created a surface that captures the loose dirt quality of a horse racing track. If you look closely, you’ll see hoof prints alongside tire tracks, which capture the unique location of this race.
kubik maltbie’s artists created a variety of samples to find the most accurate dirt display surface that’s also suitable for use in a museum setting.
Look closely and you can see evidence of horses having raced on the same track.
The next component in bringing this race to life needed to illustrate what the day was like. It also needed to convey the most exciting part—when Henry Ford overtook his competition. Working with a local artist, Glenn Barr, we created a background mural depicting Henry’s rival being left in the dust. To do this, we returned to available reference photos showing the track, grandstand, and Henry’s rival, Alexander Winton, who was the country’s most well-known racer at this time.
Sketches and small-scale paintings allowed Glenn Barr and the design team to discuss components of the mural before the final painting was created.
Glenn created a series of early sketches to make sure we had all the important elements. We then took those sketches and added them to our 3D model of the exhibition. This allowed us to pre-visualize the entire display from all angles, and verify we had the correct perspective in the mural. Color plays a big part in creating this scene with a certain mood. The goal was a color palette that felt like 100+ years ago, but also like we were watching the race. Glenn created a series of color samples that allowed us to find the right combinations.
Programs like Sketchup allow us to easily create exhibit spaces in three-dimensions so that we can study sightlines and relationships between exhibit elements.
While this photo was posed, likely to commemorate the race win, Henry Ford and Ed “Spider” Huff’s postures are confirmed from other photos, and this one provides clearer details. / THF116246
The last element in creating our day-of-the-race display was perhaps the most important—Henry Ford and his ride-along mechanic, Ed “Spider” Huff, themselves. Again, reference photos are vital tools in seeing the past. In creating these mannequins we had three key elements to address: Henry and Spider’s likenesses, the clothing they wore, and the postures they’d have sitting in the vehicle. kubik maltbie’s artists were able to capture this moment. They started with clay sculptures of Henry and Spider’s faces.
Henry Ford and Ed “Spider” Huff’s likenesses were captured in life-sized clay sculptures that would later be used to create molds for the finished mannequins.
As these mannequins needed to sit directly in the vehicle, a museum artifact, much of the final sizing, positioning, and decisions on how they interfaced with the car was done away from the actual vehicle. kubik maltbie’s sculptor came to the museum for several days and built a wood frame system around the Sweepstakes. This accurately captured important dimensions and connection points. An exact replica of the steering wheel became a template that sculptors could use in their studio to finalize hand positioning.
If you’ve visited Greenfield Village at The Henry Ford, you’ll have seen that period clothing is one of our specialties. Every spring we distribute over 1,000 sets of handmade attire authentic to many different time periods. With insight from our curators, our Clothing Studio provided period-accurate clothing, from shoes to hats, for Henry and Spider.
Henry Ford and Ed “Spider” Huff arrive at the museum.
Museum conservators and the installation team place Ed “Spider” Huff, Henry’s ride-along mechanic, on the Sweepstakes’ running board.
Together, all these elements allow us to take you on a trip back in time. I invite you to visit the museum and see this monumental moment in racing history, stand trackside, and imagine what it must have been like. You can even hear our faithful replica of the “Sweepstakes” running. It sounds nothing like today’s track-ready racing machines.
Wing Fong is Experience Design Project Manager at The Henry Ford.
cars, making, art, design, race car drivers, race cars, collections care, #Behind The Scenes @ The Henry Ford, by Wing Fong, racing, Henry Ford, Henry Ford Museum, Driven to Win
"How Are We Going to Do That?": Driven to Win Vehicle Installation
The vehicles in Driven to Win: Racing in America are displayed in a much more dynamic and contextualized way than we’ve attempted in previous car exhibits. Cars that have been displayed for decades on the floor are now elevated and (in some cases) tilted, to recreate how you would see them while racing. The payoff in guest experience will be significant, but these varied vehicle positions required extensive conversations, engineering, and problem solving between our internal teams and kubik maltbie, our fabrication partner. This post highlights four of the most notable car installations.
1965 Goldenrod Land Speed Race Car
The 1965 Goldenrod Land Speed Race Car is now displayed on a salt-flat mimicking platform just three inches high. For most vehicles, three-five people would use a couple of short ramps and push or tug the vehicle up, all in less than an hour. But for a vehicle that is 32 feet long and sits less than 2 inches off the ground, another solution had to be found—since no ramp long enough to prevent the vehicle from bottoming-out would fit in the space provided.
As a land speed racer, Goldenrod achieved its fame in miles per hour, not in turning ability. To get the vehicle anywhere besides straight back and forward, custom gantries (mobile crane-like structures) are needed to lift it off the ground so that it can turn on the gantries’ wheels, not its own. The gantries provided inspiration to solve the issue of how to raise the Goldenrod high enough to make it onto the exhibit platform.
Conservation and Exhibits staff attach gantries to Goldenrod to enable movement.
Since Goldenrod can be raised several feet once it is attached to the gantries, we were able to get the vehicle as close as possible to the platform, align it properly, then detach the back gantry and lift it onto the exhibit platform. This ability to lift the gantries independently was critical to our success.
A forklift is attached to the rear gantry and used to tow Goldenrod into position over railroad tracks covered with steel plates.
Sections of plywood and Masonite were laid to the same height as the exhibit platform. At this point, the rear gantry was rolled forward onto this temporary surface, aligned once again with its hubs.
Plywood and Masonite were used to transition the gantries to the correct height to roll Goldenrod into the exhibit.
The back gantry was then reattached to Goldenrod, allowing three-quarters of the vehicle to roll onto the exhibit platform.
Halfway there!
The same process was followed with the front gantry, and the vehicle was then adjusted into place. Steel plates and Masonite allowed the gantries to roll on the platform without damage to the faux salt surface.
Exhibits and Conservation staff celebrate Goldenrod's final placement.
Installation into the Winner’s Circle
The Winner’s Circle is the premier location in Driven to Win, showcasing some of the most renowned winning vehicles in all of motorsports, and deserves to be elevated in display. During the planning process, we first returned to our typical method of placing cars on a platform: ramps. But in this case, as with Goldenrod, not every car would have made it up a ramp with the pitch necessary, due to other exhibit items in the way. We went back and forth from idea to idea for some time.
What we finally settled on was what we’ve deemed “rolling jackstands,” or dollies. kubik maltbie took our measurements of these vehicles and fabricated these dollies out of Unistrut and casters. Each was custom-fitted and modified on site to conform to the load when the car was rested on top of them. Once on these dollies, the cars are very easy to move. They slide into the Winner’s Circle and the fronts of their platforms slide into place in a theatrical, modular way.
Custom dollies, or "rolling jackstands" allow vehicles to be elevated for display and rolled into the exhibit at the appropriate height.
By this point, half of the problem was solved. The other half was how to get these cars onto their jackstands. For this, we employed three techniques. First, we were able to sling some of the cars and lift them using a huge gantry on the back half and a forklift on the front. We used this method on the 1958 Moore/Unser Pikes Peak Hill Climb Racing Car. It was a slow but effective means of raising the vehicle just high enough that the jackstands could be slid underneath.
1958 Moore/Unser Pikes Peak Hill Climb racing car being lifted using a gantry and forklift.
One vehicle, the 1956 Chrysler 300C Stock Car, had the ability to be lifted from below using floor jacks.
1956 Chrysler 300B Stock Car rolling into its display position.
Finally, some vehicles, including the Indy cars and the 1967 Mark IV Race Car, posed serious issues since they had nowhere that we could use a floor jack, and did not have bodies that could be slung with straps.
In this case, we benefited from having an expert volunteer on our team. Mose Nowland was one of the original engineers who built the Mark IV in the 1960s. A fantastic problem-solver, he designed a custom metal apparatus, which we call a “sling,” that would allow a telescopic handler to lift it. We had Mose’s design fabricated at a metal shop. Since the sling spread out the attachment points, straps could then be placed and balanced at appropriate points on the vehicles. It really helps to know one of the car’s original engineers when you need to figure out rigging stunts like this.
Mark IV being lifted onto its dollies with the help of a custom sling and a telescopic handler.
But what if we wanted some of these elevated cars to be on an angle, like they would be while actually racing? First, we needed to have that approved by a conservator, to make sure the car can physically handle years or decades in that position. Then, the same lifting methods described above were used, but the rolling jackstand dollies were made with legs of various heights. When the cars were set down upon them, they were strapped in with custom mounts so that they could sit comfortably for much time to come.
Ultimately, the goal of any artifact mount is to safely hold the object but not call attention to itself. We hope that we’ve succeeded in keeping the emphasis on an exciting presentation of these vehicles that we are looking forward to showing our guests.
The 1958 Moore/Unser racing up our scenic recreation of Pikes Peak in Driven to Win.
The Mark IV on permanent display in Driven to Win.
Kate Morland is Exhibits Manager at The Henry Ford.
race cars, Mark IV, racing, Henry Ford Museum, Driven to Win, collections care, cars, by Kate Morland, #Behind The Scenes @ The Henry Ford
Improving Accessibility and Inclusion
Adult changing table in one of our two new accessible companion-care restrooms.
As for so many others, the year 2020 was not easy for The Henry Ford. The pandemic brought many challenges that we had to face as an institution. Despite those challenges, we remained committed to reaching strategic goals that we had set to improve accessibility and inclusion for all of our guests. Through teamwork and determination, we were able to stay on track toward this commitment.
We are excited to share that we received a three-year grant from the federal Institute of Museum and Library Services (IMLS) to support sensory programming initiatives. With this grant, we will be able to expand our current programming and build on what we have learned with new programming for guests with autism spectrum disorder (ASD) and sensory processing disorder (SPD). The grant will allow guests to have improved on-site experiences and access to our collections in all of our venues.
Another aspect provided by the grant is free general admission to families of those with ASD and SPD. Two of our special events, Sensory-Friendly Hallowe'en in Greenfield Village and Sensory-Friendly Holiday Nights in Greenfield Village, are included. In 2020, we hosted 875 guests for those very popular events.
In addition, we are excited to announce that, within the next year, we are planning to launch a new program for teens and young adults with ASD and SPD that will include activities aimed at social skill-building and networking.
The inclusion of all guests is one of the main pillars of our strategic plan. We believe that this is an important component that will help all guests feel welcome and comfortable on our campus. Because of this, we are expanding training for both current and new staff members. We are developing a module that will use information from the Autism Alliance of Michigan, as well as other organizations, to help our staff become more aware of those with disabilities. As an institution, we understand that it is our responsibility to become more aware of disabilities, as well as how we can modify our unique educational experiences for guests who may need additional support. It is important that guests of all ages, backgrounds and abilities have equal access to the collection and our campus.
Another example of how we are making a more comfortable experience for our guests with disabilities is with the installation of two new accessible companion care restrooms, located at both ends of the main promenade of Henry Ford Museum of American Innovation. Our accessibility specialist, Caroline Braden, partnered with the Madison Center to help design these restrooms. The Madison Center has partnered with The Henry Ford for over 10 years through our Community Outreach Program. The project was supported in part by grants from the Michigan Council for Arts and Cultural Affairs and the Ford Foundation.
Toilet in one of our new accessible companion-care restrooms.
The work done on the companion care restrooms goes above and beyond compliance with the Americans with Disabilities Act. The restrooms are barrier-free and include power-operated doors, extra space, and a power-adjustable adult changing table. These tables will be able to accommodate guests with physical and cognitive disabilities. As an institution, we are very proud of this construction, and we are very grateful to those who worked so hard on this essential project.
Caroline Heise is Annual Fund Specialist at The Henry Ford.
by Caroline Heise, The Henry Ford Effect, IMLS grant, Henry Ford Museum, design, accessibility, #Behind The Scenes @ The Henry Ford
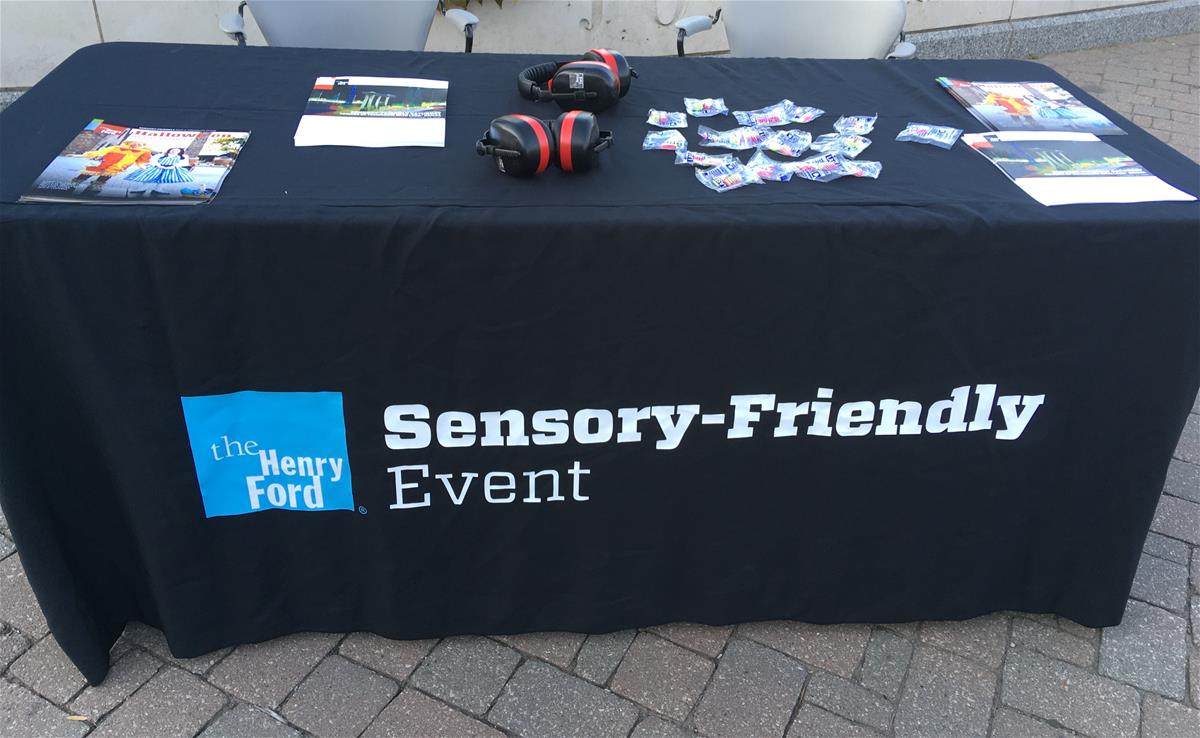
Sensory-friendly event entrance table.
For nearly 20 years, The Henry Ford has sought to provide safe, unique, and engaging experiences for our members and guests on the autism spectrum and their families. It has been a long journey, with a slow start and a positive twist during a worldwide pandemic in 2020, an otherwise extremely challenging year. We are pleased to share with you a brief history of our efforts and an exciting announcement about opportunities for future visits to The Henry Ford.
Early efforts at specialized programming began in 2000 with a partnership event with the Autism Society of Michigan during one of our first Day Out With Thomas events and later with safety trainings led by the Autism Alliance of Michigan (AAoM). Guest-facing staff and security personnel were trained on the impacts of autism spectrum disorder and sensory processing disorder (ASD/SPD) and given basic instruction on how to interact with caregivers and assist in keeping these guests safe while visiting. The focus was on improving service and engagement for guests with ASD/SPD who were already visiting, not necessarily on drawing more families and guests with ASD/SPD to our venues and programs.
Sensory-friendly entrance sign in Henry Ford Museum of American Innovation.
By 2015, our desire to serve more guests with disabilities had evolved into concrete initiatives and plans with the addition of Caroline Braden, now our full-time accessibility specialist on the Guest Services Team. Caroline's background in museums and accessibility programming allowed us to build and deliver a broad range of services, programs and accommodations designed for guests with disabilities, both on-site and online. I personally have had the privilege of working with Caroline and many outstanding partners and colleagues who have contributed to the growth of accessibility programming over the years. Additionally, this work has been a personal passion, as my youngest child has been diagnosed with ASD.
At The Henry Ford, our current sensory-friendly programming began in 2016. Since then, we have had at least three or four sensory-friendly events a year. These events have included such offerings as pre-visit materials (i.e., social narratives), sensory-friendly maps, noise-canceling headphones and earplugs, quiet zones, and turning loud sounds down or off. We have also offered exclusive access times to some of our exhibits and events, such as our Hallowe'en in Greenfield Village event—one of our most popular sensory-friendly events of the past few years.
Sensory-friendly entrance sign at Hallowe'en in Greenfield Village.
Which brings us to our exciting news and the most positive twist in this story—a substantial grant that The Henry Ford received this past fall from the Institute of Museum and Library Services (IMLS). This grant will enable us to significantly expand our current sensory-friendly programming to provide access to over 18,000 guests with ASD/SPD and their families within the funding period of three years.
To do this, The Henry Ford will increase the number of sensory-friendly events to 13–15 a year, including more access and accommodations for our special annual events. We will also develop and launch a new program for teens and young adults with ASD/SPD that will include activities aimed at social skill-building and networking. This programming will include not only the successful access and accommodations we have provided in the past but free admission as well, removing any unique economic and/or social barriers.
As an additional component of the grant, we are developing new training for staff in partnership with AAoM. This training, combined with the yearly safety training from AAoM, will be designed to broaden awareness and develop programmatic and service skills around the unique needs of those with ASD/SPD.
The timing of this grant during the COVID-19 pandemic has made our delivery of sensory-friendly programming more complex. As safety is our number one priority, The Henry Ford is operating at 25% of normal venue capacities, and some venues and programming are not available at all. IMLS, however, has been extremely flexible in allowing us to modify our on-site programming and move certain aspects to virtual programming. For updates on virtual opportunities and onsite events in 2021, continue to follow The Henry Ford’s social channels and website.
Amy Louise Liedel of The Henry Ford receives AAoM’s Seal of Approval from AAoM President & CEO Colleen Allen.
We are also proud to have recently received AAoM’s Seal of Approval endorsement. The endorsement is given by AAoM to businesses and organizations in Michigan who demonstrate a conscious effort to accommodate and include individuals with autism in community activities that all families enjoy.
We look forward to continuing to expand our sensory-friendly offerings and hope to see you soon at The Henry Ford.
Amy Louise Liedel is Senior Director of Guest Operations at The Henry Ford.
Greenfield Village, Henry Ford Museum, events, IMLS grant, #Behind The Scenes @ The Henry Ford, COVID 19 impact, by Amy Louise Liedel, accessibility
Print-at-Home Holiday Gift Tags
My name is Cheryl Preston, and I’m a graphic designer and design director at The Henry Ford. What I get to do here is design graphics for print and online use—design to educate teachers and learners, market events, support the stories we tell, sell food experiences, tempt shoppers, and guide visits around the museum, village and factory tour. I get to combine two passions, history and design, in one job.
2020 Ballotini Ornament, combined with a gift tag.
We all know 2020 has been crazy and difficult in many ways. I have been working on this year’s digital-only holiday retail campaign, where we are featuring a lot of new and old favorite signature handcrafts, along with fun, innovative toys. This has been a bright spot in tough pandemic times for me right now.
It got me thinking how we still love to gift friends and family. After you’ve found the perfect collectible glass candy cane, or an overshot woven placemat set, made in the village weaving shop, which will look great on your friend’s table, you have to wrap it!
Overshot Placemat, combined with gift tags.
I wanted to create a tiny bit of “happy" to give our supporters, with these free printable gift tags to bring the cheer. We all need even the tiny smiles, right? You can preview the gift tags below, or click here to download a PDF version of them for printing at home.
I’m in awe of the handcrafts from our Greenfield Village artists, and the products we offer to bring the past forward, and hope these tags help you share the fun!
Cheryl Preston is Design Director at The Henry Ford.
21st century, 2020s, shopping, making, holidays, design, COVID 19 impact, Christmas, by Cheryl Preston, #Behind The Scenes @ The Henry Ford
#Digitization100K: Wrap-Up and Round-Up
Throughout the month of November 2020, we’ve been celebrating reaching the milestone of 100,000 digitized artifacts by sharing out blog posts and fun facts, hosting Twitter chats with our digitization staff, and counting down the 20 most-viewed artifacts in our Digital Collections. In case you missed any of these great resources, we wanted to share them all here for easy reference.
If you follow us on social media, you might have seen the “top 20” countdown of our most-viewed digitized artifacts of all time, but if you’d like to get a broader look, you can check out the top 100 in this Expert Set. Fans of The Henry Ford will recognize many of the artifacts, but there may be some on the list that surprise you.
The Henry Ford's all-time top 20 most-viewed digitized artifacts. Do any of them surprise you?
Here, also, are all of the fun facts about our digitization program and our Digital Collections that we shared out on social media.
Twenty fun facts about digitization and our Digital Collections.
During the first week of November, we provided a general introduction to our Digital Collections, our digitization program, and our workflows.
- First was our announcement that we had just digitized our 100,000th artifact, and were kicking off the month-long celebration. You can also read our press release here.
- If you’re interested in becoming an expert in using our Digital Collections, or just not sure where to start, this blog post will give you a run-down of the ways you can search, view, and use our digitized artifacts.
- Associate Curator, Digital Content Andy Stupperich shared how we add context to artifacts in our Digital Collections in this post.
- Saige Jedele, also an Associate Curator, Digital Content, took us behind the scenes with The Henry Ford’s Innovation Nation to discover how digitization helps shape the stories we cover on the show--and helps you to learn more afterwards.
- Like many other people around the world, a lot of our staff have spent time this year working from home. Find out how we continued to digitize artifacts despite the closure of our campus this spring in this post.
- As part of the William Davidson Foundation Initiative for Entrepreneurship, we've digitized nearly 2,500 artifacts from our collections. Find out more about the team and the process from Project Curator Samantha Johnson here.
- In our first live Twitter chat on November 5, I discussed our digitization program, digitization workflows, and a bit about what you'll find in our Digital Collections.
2020s, 21st century, research, photography, digitization, digital collections, conservation, collections care, by Ellice Engdahl, #digitization100K, #Behind The Scenes @ The Henry Ford
A Puzzle Block Surprise
In 2017, I had the opportunity to work with our curator of domestic life, Jeanine Head Miller, on a new Expert Set featuring alphabet blocks and spelling toys from our collections. We chose one example based on a nearly 20-year-old photograph from our collections database. It was dated between 1860 and 1880 and appeared to be a set of wooden alphabet blocks with images printed on the reverse that could be assembled to complete two puzzles. Notes in the database and an image on the box lid alluded to more, so we decided to re-photograph the blocks before adding them to our Digital Collections.
Image taken in 2000; touched up in 2017 by Jim Orr, image services specialist / THF133429
While conducting research for the Expert Set, I visited our photographic studio to see the blocks in person. They were in good condition, and I was able to carefully – with gloves and on a clean surface – assemble each of eight possible solutions, revealing not only the alphabet and two 12-block puzzles visible in our existing photograph (“The Farm” and “Anna’s Delight”), but two other pastoral scenes of the same size (“Grandfather’s Visit” and “My Country Residence”), two full-size, 24-block historical images (“William Penn’s Treaty with the Indians” and “Mount Vernon – Washington’s Residence”), and a map of the United States. The borders and place names on the map gave us hope that we might be able to narrow the date range for these blocks, but some text on the Mount Vernon puzzle gave us an even better clue – the lithographer’s name!
Reference image showing lithographer information [REG2017_1103]
A quick Internet search (an invaluable tool for modern museum research) revealed that Thomas S. Wagner worked as the sole proprietor of his Philadelphia lithography firm for a short time, between a dissolved partnership with fellow lithographer James McGuigan in 1858 and Wagner’s death in 1863. (Interestingly, according to the Library Company of Philadelphia, Wagner was “one of the few publishers of wooden lithographic puzzles” at that time.) Not only were we able to considerably narrow our date range from 1860–1880 to 1858–1863, we could now add creator information to our records!
We decided to have our photographer, Rudy Ruzicska, and digital imaging specialist, Jillian Ferraiuolo, create just a few official images of the picture puzzle – enough to document the box and individual blocks and to give online viewers a sense of the possible solutions. But I also captured reference photographs of each of the 8 completed puzzles for our collections database. These wouldn’t typically be available to the public, but to celebrate our recent digital collections milestone – 100,000 artifacts! – I’ve shared a few of them below.
Thanks for reading!
Continue Reading
Pennsylvania, 19th century, toys and games, photography, digitization, by Saige Jedele, #digitization100K, #Behind The Scenes @ The Henry Ford
Photographing Large Artifacts on Location
My name is Jillian Ferraiuolo and I’m a Digital Imaging Specialist at The Henry Ford. In that role, I work with our institutional photographer in our Photo Studio, taking photographs of artifacts and preparing those for use in our Digital Collections.
This graphic shows where photography fits into The Henry Ford's overall digitization process.
Every once in a while, our job requires us to step out of the studio, equipment and all, and photograph artifacts on location. Whether it’s taking photos of cars in one of our storage buildings or taking photos in (or of!) one of the buildings in Greenfield Village, if it can’t fit inside the studio, then we pack up and go to it. For example, the geodesic truss pictured below is in storage, but we needed to photograph it. You can see from the photo below how large it is, so instead of trying to find some way to get it to the Photo Studio in the museum, we went to it.
Photography staff and volunteers shooting the geodesic truss on location at a storage building.
The finished product: Geodesic Dome Test Module, Designed by R. Buckminster Fuller, 1953. / THF166740
One of the biggest challenges for us when we shoot outside the studio is making the most of our time. Given how large our campus is, we try to be as efficient as possible while still creating the same shooting environment on location as we would in the studio, especially when it comes to lighting and image quality. Another challenge of location shoots is that they allow less freedom than being in the studio—some objects are in a specific spot and can’t be moved or adjusted. When we’re in the studio we can change angles, move lights, and make adjustments easily, but if we’re out photographing a train car, and need to capture a different view, we have to move around it—there’s no way it’s moving!
Another example of getting creative to photograph a lathe used by Henry Ford out at the Bagley Avenue Workshop in Greenfield Village.
While shooting out on location can be a challenge, it is also a nice change of pace and a nice change of scenery. It forces us to think outside the box and get creative with taking photos—especially when the shoot involves something outside the norm. Take, for example, quilts—since they’re so large, we have to get up much higher than they are so we can get an accurate photo of the entire quilt. (You can read more about our quilt photography process here.)
Getting ready to photograph quilts from the Highland Park Engine catwalk in Henry Ford Museum of American Innovation.
But whether we’re in the studio or not, we’re passionate about what we do, and we are ready to take on any challenge!
Continue Reading
by Jillian Ferraiuolo, #Behind The Scenes @ The Henry Ford, #digitization100K, digitization, photography
Ford Motor Company Part Drawing Collection, 1903-1957
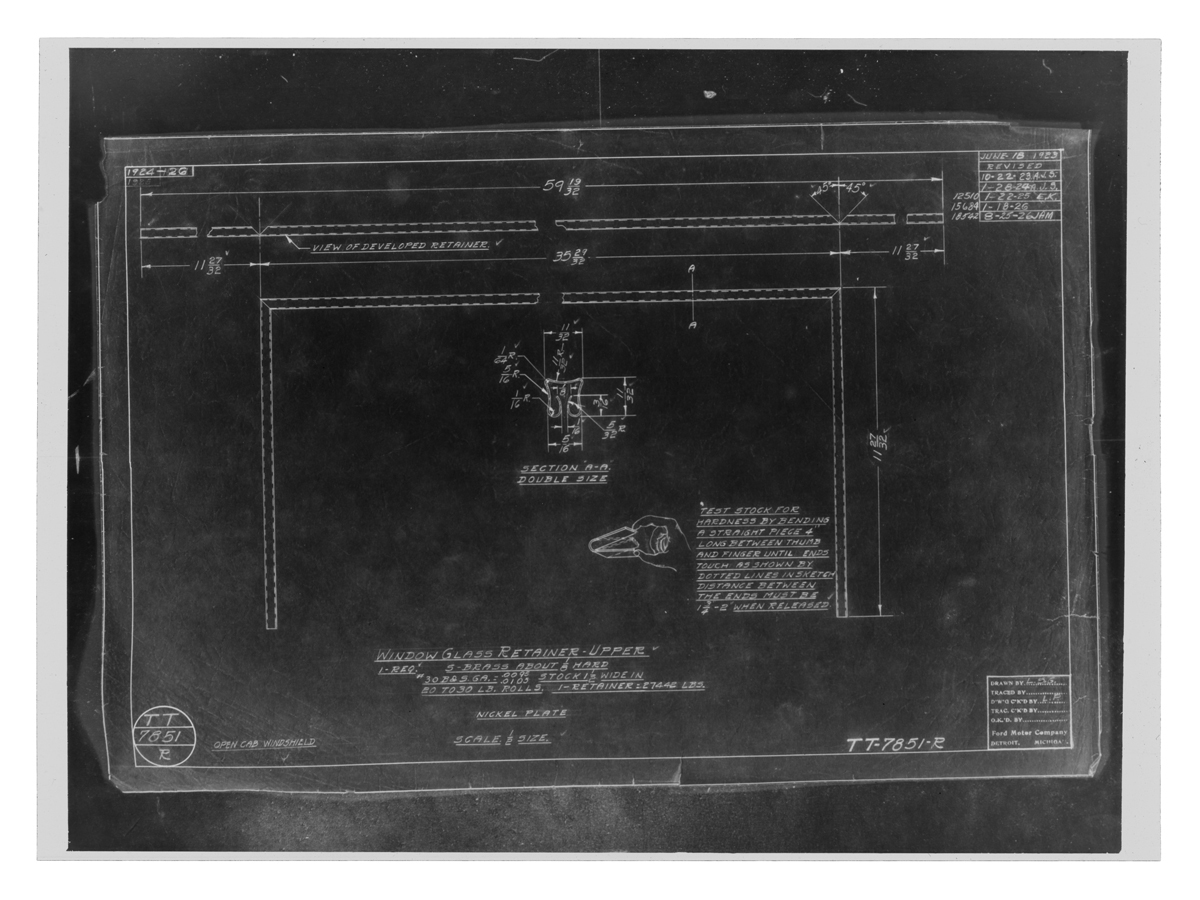
By the early 1950s, Ford Motor Company’s engineers had made over one million technical drawings of the parts used to make Ford cars and trucks. In 1949 alone, they used 13 million square feet of blueprint paper!
Ford Motor Company engineers at work, circa 1952. / THF125069
The drawings were being stashed away wherever room could be found. Since many of the drawings were for parts that were still in production, there was concern that the company’s operations would come to a halt if drawings were lost to a fire, a flood, or worse. Plans were made to microfilm the drawings so they could be stored more securely.
Paragraph from a 1951 brochure detailing the microfilming project. Cold War tensions were running high. / detail from THF135511
Eleven fireproof storage safes, holding one million microfilmed drawings, 1951. / THF123713
To save space, most of the original paper blueprints were destroyed after the drawings were copied onto microfilm. But a few can still be found in our Miscellaneous Ford Motor Company Blueprint and Drawings Collection.
Blueprint showing part TT-7851-R for a Ford Model TT Truck. / THF138486
70 mm microfilm copy of the same drawing. / THF406917
The Ford Motor Company Part Drawing Collection consists of over one million Ford engineering drawings from 1903–1957, on 70 mm microfilm. Each piece of film measures approximately 2.625 x 3.5 inches, and is in a manila envelope that shows the part number and the drawing’s latest revision date.
Envelope for drawing TT-7851-R, dated August 25, 1926. / THF406916
As of this writing, about 3,000 Ford part drawings can be seen on our Digital Collections website. Only 997,000 to go!
So, why don’t we “just” digitize them all?
The first challenge is the size of the film. Most high-speed scanners on the market now are not equipped to hold 70 mm film. And because each frame of film was cut from its roll and placed in a separate envelope, the film cannot simply be run through a machine.
We image the film using an Epson Perfection V850 Scanner with built-in Transparency Unit (a light inside the lid that allows it to scan film). Each piece of film measures just under 3 x 4 inches, so a scanning resolution of 1200 dpi (3600 x 4800 pixels) will usually suffice … but we go higher if a drawing looks like it will be difficult to read.
Larger blueprints, like this one for a V-8 Cylinder Block, were microfilmed in segments. / THF401366
After the film has been scanned, the images are straightened and cropped, and adjustments may be made to the brightness and contrast. If the film is a negative, we also create an additional, positive version of the digital image.
This version of the digital image can be printed without using as much toner. / THF406918
However, the bigger challenge is the data entry. Even the best digital image is useless if nobody can find it. To that end, it is necessary to transcribe the part number, the date of the drawing, and the title of the drawing from each piece of film. And many of the drawings include more than one part number!
If parts are symmetrical opposites, there is only one drawing for the pair. / detail from THF400831
The revision history appears in the upper right corner of each drawing. This drawing is dated December 3, 1930 … but earlier versions may also exist. / detail from THF400831
If you are interested in researching the Ford Motor Company Part Drawings Collection, our Popular Research Topics page includes an FAQ and information about how to get started. Inquiries can be sent to research.center@thehenryford.org.
The Henry Ford is facing unprecedented financial challenges due to the impact of our 16-week closure and reduced operations. We need your help in securing our future. Love the Henry Ford? Please support all that we treasure—including our digitization program. Longtime supporters of The Henry Ford will match your donation dollar for dollar, so your contribution will have double the impact. |
20th century, Ford Motor Company, drawings, digitization, cars, by Jim Orr, archives, #digitization100K, #Behind The Scenes @ The Henry Ford
Building and Operating a Highland Park Plant for the Digital Age
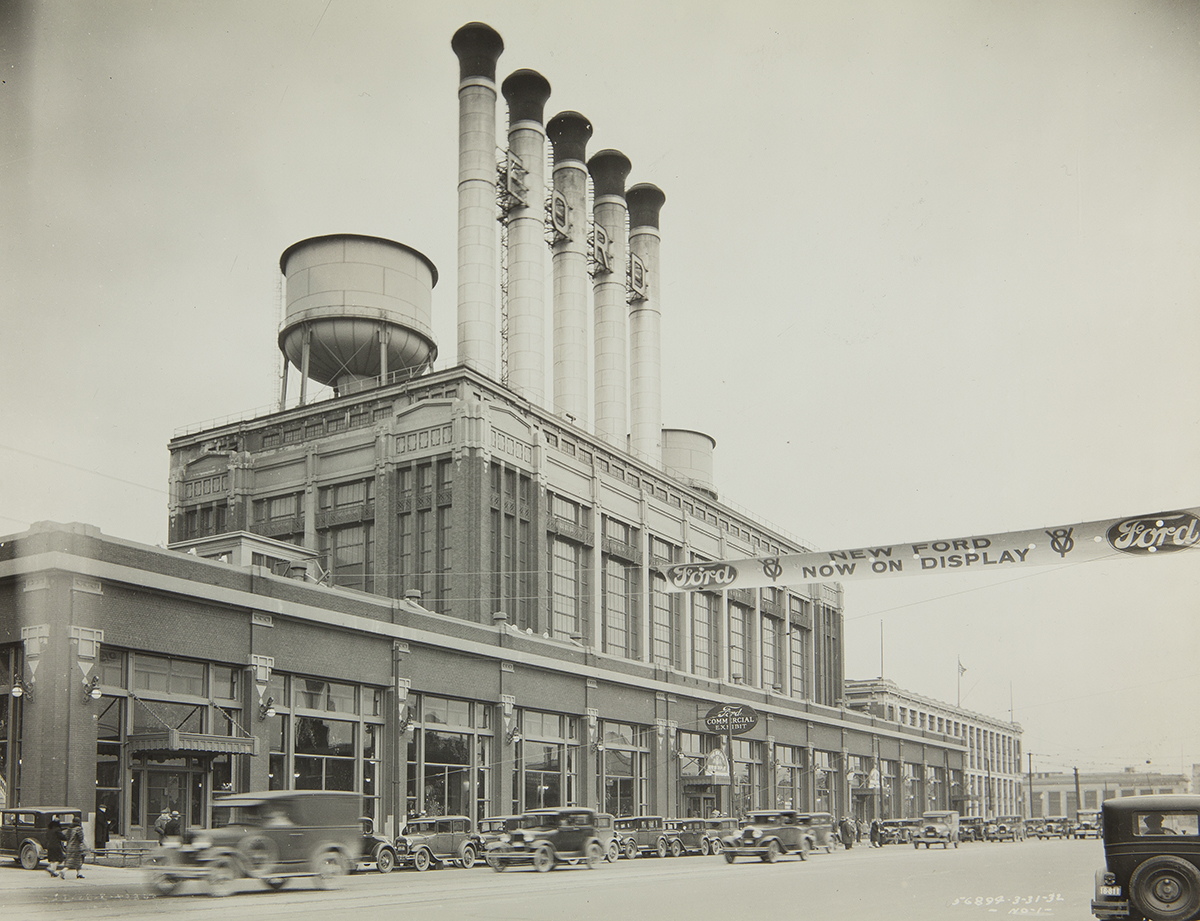
Exterior View, Ford Highland Park Plant, 30 March 1932; Object P.833.56894.1 / THF237509
When Ford Motor Company engineers developed the assembly line at the Highland Park Plant back in 1913, they were seeking to increase production volume in order to provide more automobiles to the general public at a reasonable cost, and in a reasonable time.
Move ahead more than 100 years to 2020, where the staff of The Henry Ford and the Benson Ford Research Center (BFRC) are operating a modern assembly line to digitize images and documents from our collections and make them available online.
By some estimates, The Henry Ford holds roughly 26 million 2D and 3D objects, with the majority of that total – some 25 million items – contained within the archival collections at the BFRC. Clearly, there’s a lot to move down our “assembly line”!
As is the case with auto assembly, there are a number of stations along our line, beginning with material selection, then material retrieval, cataloging, imaging, storage, import, export, and finally ending with online display. Improvements made to the speed and efficiency at each of these stations can lead to gains in the production rate of the entire line.
This graphic shows where Rapid Capture imaging fits into The Henry Ford's overall digitization process.
To bring that speed and efficiency to archival imaging, the BFRC uses a process we refer to as Rapid Capture digitization. Developed by several institutions as an approach to increasing the scale of digitization, Rapid Capture is part technology, part process, and part philosophy.
Technically, Rapid Capture is rather simple. The equipment consists of a copy stand, lighting, a digital single lens reflex (DSLR) camera, and a computer equipped with photo editing software.
Rapid Capture station.
The important feature of the camera is its full-frame sensor, which can create a 400-pixel-per-inch image of an item as large as 9 × 14 inches, allowing us to provide users with high-quality images for the majority of our archival materials, which can be easily viewed, downloaded, and used for presentations or reports.
At the click of the shutter button, the camera can record an entire image – perhaps an 8 × 10 photographic print – without the cycle time of a more traditional flatbed scanner. If you’ve used a digital camera or a camera phone to take personal photographs, then you know how quickly you can take tens or even hundreds of snapshots. The same holds true for Rapid Capture, with the limit on imaging rate being the safe and proper handling of the archival material, not the time spent waiting for the scanner to make a pass.
On certain projects, we are able to capture both sides of a photographic print in less than 60 seconds, translating to nearly 500 prints imaged in a single day. Our flatbed scanner can produce 10-12 images per hour, or both sides of just 48 prints per day. Starting with a single Rapid Capture workstation in February 2011 and now utilizing two workstations, we have produced nearly 100,000 production images since the launching the process.
Process, or efficiency in process, is also an important part of Rapid Capture. For example, since material handling is one of the keys to the speed of Rapid Capture, we work to select and schedule material in groups having similar sizes or formats and that are located together physically, such as the box of 8 × 10 photographic prints shown below.
8 x 10 photographs from our collection foldered within an archival box.
Another example occurs in the post-processing of images, which can also be done in a batch manner, including exposure correction, cropping, and derivative image creation. By using automated scripts, much of this work can be done unattended, and in the case of large batches, performed in the overnight hours.
Finally, Rapid Capture is in some ways a philosophy. Rapid Capture puts a premium on user access to large numbers of images, and in doing so forces trade-offs in areas such as perceived image quality and image resolution. An example of this trade-off can be seen in some of our Rapid Capture images, which appear slightly tilted, such as this image from the Detroit Publishing Company Collection.
Railway Station at Haines Corners, Catskill Mountains, New York, circa 1902; Object P.DPC.014510 / THF204908
Rather than spend additional time on each image to create a perfect alignment, we’ve chosen to spend that additional time producing more images, with the assumption that you, our users, would want to see more “stuff,” and can accept some imperfection.
A second compromise involves image resolution. While the camera can produce images sufficient for online viewing and use in presentations, the images may not be adequate for advertising or commercial publication. We’ve accepted that a certain number of items may need to be reimaged at some point for publication use, but that the potential rescanning effort is outweighed by the ability to both produce and store more lower-resolution images.
Our implementation of Rapid Capture has proven to be very successful. In nearly 10 years of operation, we’ve created a large number of images that meet our goals for quality, usefulness, production time, and cost. And, as we celebrate our #digitization100K milestone of 100,000 digitized objects on our Digital Collections, we can also point to the more than 38,500 objects that are illustrated using Rapid Capture images as another measure of that success.
Continue Reading
digital collections, by Brian Wilson, #Behind The Scenes @ The Henry Ford, #digitization100K, digitization, archives, photography, technology